Dansko using robots to make distribution center more efficient
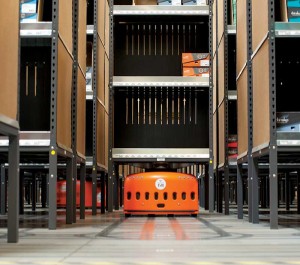
With its giant new distribution center in West Grove, Dansko was going to need more than just more workers to keep track of products going in and out. A Kiva® robot follows bar codes on the floor to locate the specific product needed to fill an order.
WEST GROVE — Driving along Jennersville Road (Rt. 796) in southern Chester County, anyone familiar with the surroundings has noticed the new, large industrial building sitting well off the road. Very attractive, especially considering its size, the building bears the name of one of the area’s most recognizable and respected businesses, Dansko.
What the average passerby doesn’t know is that something else shares the 200,000 square-foot building with the company’s renowned footwear – robots.
Despite the common worry that workers will be replaced by robots, these “bots.” as they are referred to at Dansko, aren’t taking anyone’s job. In fact, since the distribution center opened in Nov., 2012, additional employees have been added to the warehouse team, bringing the current number of Dansko employees to about 185. The distribution center team, which works one and a half shifts, is responsible for receiving all shipments of Dansko footwear that arrive at Dansko from Europe and Asia. Once received, the shoes are packed and shipped to over 2,500 retailers.
Chief Operating Officer Mimi Curry admits there were definitely tense moments and bugs to be worked out when the new distribution center “went live” in November.
“We spent many nights here,” she adds with grin. “Every day we were learning new things, and now we are still making subtle changes that are coming from the operators. The entire team has brought suggestions for tweaking and improving the process and the system.”
Curry says planning for the new distribution center actually began about five years ago as Dansko founders, husband and wife, Peter Kjellerup and Mandy Cabot, knew they were outgrowing their current facility and sought a solution that would carry them for the next 10 years. By the time the new distribution center was complete, Curry was shuffling stock from the existing 80,000 square-foot warehouse, two off-site warehouses and 15 trailers.
“It was very inefficient,” she says.
Experts were consulted on the feasibility of expanding at their current location, but they concluded there just was not enough room. Kejellerup and Cabot were determined to build a state-of-the-art facility that not only would meet their projected needs, but would also be in keeping with Dansko’s commitment to minimizing their environmental footprint. They found a piece of commercial property very well-suited to their needs in close proximity to their corporate headquarters in West Grove.
Kjellerup, passionate about the environment long before “green” became a buzzword in this country, is Dansko’s “eco” champion. His enthusiasm and mission to make a mark with their shoes and not their footprint are evident throughout the company.
“To construct a building in an environmentally responsible manner may not be the easiest or cheapest way,” he notes. “We never considered not doing the right thing. For us, there was simply no alternative to making the best use of our natural resources and being responsible in our design, construction and material choices,” he insists.
In keeping with the Gold LEED® (Leadership in Energy and Environmental Design) certification Dansko received for its corporate headquarters building in 2008, they planned the distribution center project with an eye to LEED® certification as well. Daria Payne, facilities manager, explains that it is much more difficult to attain LEED® certification from the U.S. Green Building Council for an industrial-type building like the distribution center simply “because of the type of space it is, primarily a warehouse.”
In the corporate office there were a lot of opportunities to include features such as modular carpet tiles, easy-to-clean flooring made with 100% post-use recycled glass, and locally sourced and recycled components such as the eco-resin panels, counters from recycled materials and locally sourced cabinets. These same components were used in the office part of the distribution center however; they represent a smaller percentage of the overall square footage of the building.
Payne is eager to submit Dansko’s LEED® scorecard in the class for new construction and expects to do so by the end of August. She outlines the various categories in which an applicant can earn credits that are then totaled to determine if a building ranks as certified, silver, gold or platinum. While Payne explains that credits in some of the categories, including brownfield development credits and credits for access to public transportation are out of reach for the distribution center based on location and the type of building, she looks to excel in categories that are more feasible for their particular project. For example, in the energy and atmosphere category she expects to receive good scores for optimizing energy performance and on-site renewable energy.
Both the corporate headquarters as well as the new distribution center utilize large solar panel systems providing about 30% of Dansko’s total energy needs. Their solar energy is supplemented with wind energy credits making 100% of the energy used at Dansko renewable. The extensive stormwater management system at the distribution center, as well as the natural light provided by skylights, should result in maximum LEED® credits as well. “We’ve also re-used materials where we could, like office furniture and some of the racking system,” Payne emphasizes.
While Payne worked diligently on the building structure, Curry’s job was to create effective packing and shipping processes for the distribution center. Well before the construction of the distribution center began, Curry and Kjellerup explored systems that could increase the efficiency. Obviously, the time to put such a system in place would be while the initial construction was taking place. One company, Kiva® Systems, stood out as a leader in field of warehouse automation. Kiva designs order fulfillment systems that use mobile robots. Their clients include diapers.com, Staples, Walgreens, Crate and Barrel, and GAP. Shortly after the completion of Dansko’s system, Amazon.com acquired Kiva. “We lucked out in our timing,” says Curry explaining that Amazon would not permit Kiva to take on any new jobs until their own warehouses were equipped with Kiva systems.
In Dansko’s case, Kiva installed 46 robots that are directed by operators as to what items they need to fill an order. Communicating wirelessly with operators using order-processing software, the “bots”, equipped with onboard cameras, follow bar codes on the floor to locate and retrieve one of the 970 pods in the system containing the specific product needed for an order.
The Kiva system allows an operator to work on six orders at a time. “Previously, the pullers had to go and get the shoes; now the shoes come to them,” Curry says. She explains that on average a worker who pulled product for orders would walk 6 to 8 miles a day in the process.
Curry relays a story depicting the impact of the Kiva system at Dansko. “We have a woman who has worked here over 10 years. She was very opposed to the new system, basically fearing change,” she explains. “A couple of months into it I asked her how she was doing and what she thought of the system. She smiled and told me that she now has more energy after work to have fun, go out with friends, and to play with her grandchildren; something she previously found difficult after walking all day.”
Having worked at Dansko for 16 years, Curry knows well the importance of keeping their employees healthy and content. Through its foundation, Dansko encourages employees to give back to their communities and passions by providing paid time off for up to 20 hours of volunteer time. Recently, an Employee Stock Ownership Plan, replacing one that provided partial ownership to employees since 2003, was implemented, making Dansko a 100% employee-owned company.